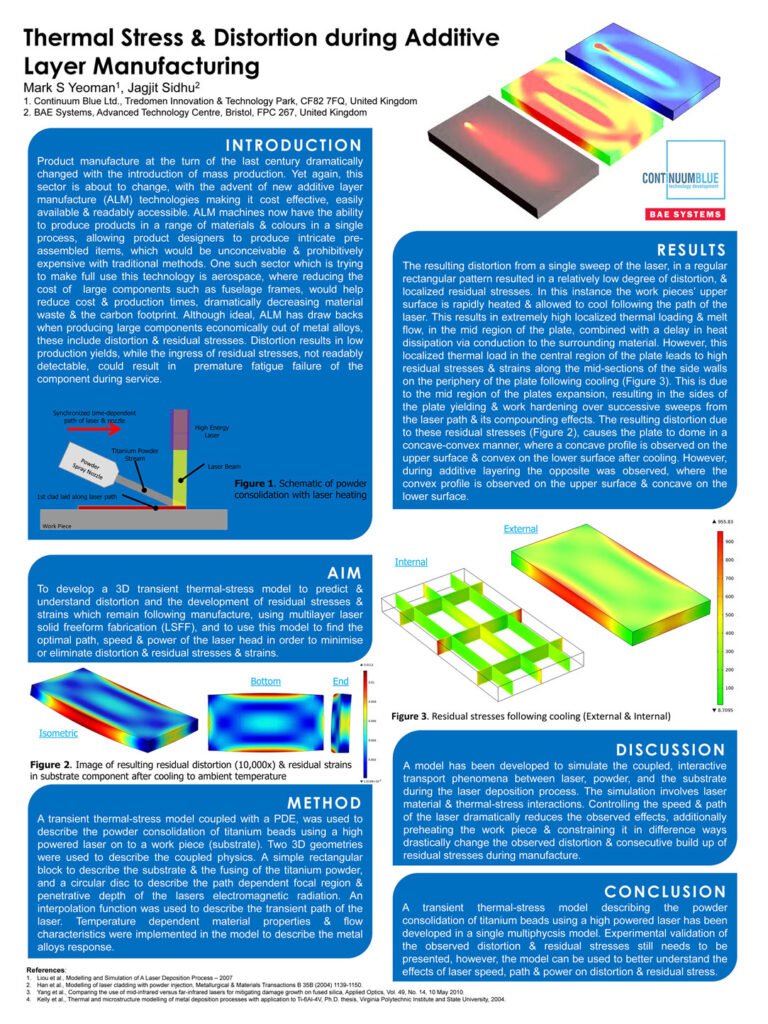
Additive Layer Manufacturing (ALM), also known as additive manufacturing, 3D printing, or rapid prototyping, is a process of creating three-dimensional objects by adding layers of material one upon another. It is a process where a computer-controlled machine creates a 3D object from a digital design, using various materials such as plastics, metals, ceramics, and composites.
ALM technology has many advantages over traditional manufacturing methods, such as reducing waste, enabling the development of very complex geometries, allowing for rapid prototyping, and customization. ALM is used in a wide range of industries, from aerospace and automotive to medical and consumer products. When designing parts for additive layer manufacturing of metal alloys, there are several critical design characteristics to take into account, such as:
- Support Structures: In metal additive manufacturing, support structures are needed to anchor the parts to the build plate and support overhanging features during printing. The orientation and placement of these structures can have a significant impact on the final part’s surface finish, dimensional accuracy, and printing time.
- Part Orientation: The orientation of the part during printing can have a significant effect on its properties, as it can impact the heat transfer and residual stresses that develop during the printing process. Certain orientations may lead to distortion or warping of the part, whereas others may enhance mechanical properties.
- Wall Thickness: Wall thickness is an important consideration in metal additive manufacturing, as thinner walls can lead to faster printing times and reduced material usage. However, thicker walls can provide greater structural stability and durability.
- Powder Bed Fusion Parameters: The specific parameters of the metal powder bed fusion process, such as laser power, scan speed, and layer thickness, can impact the part’s surface finish, porosity, and mechanical properties.
- Material Selection: The selection of the metal alloy used in additive manufacturing is critical, as different alloys have different material properties and printing requirements. It is essential to select an alloy that is compatible with the printing process and that can meet the required performance specifications.
- Post-Processing Requirements: Finally, it is important to consider the post-processing requirements of the printed part, including heat treatment, surface finishing, and machining. These steps can significantly impact the part’s final properties and must be carefully planned during the design phase.